29%
Decrease in energy consumption since 2001 baseline
Renewable
We self-generate 100% of our energy use
1st
First Smart Lab campus in New England
Energy
UNH implements a systematic and integrated energy policy that emphasizes health and integrity, climate protection, efficiency, cost-effectiveness and stability, fairness for all University constituents, and consistency with priorities set by the UNH Strategic Plan and UNH Campus Master Plan.
For over 25 years, the University of New Hampshire has explored and demonstrated renewable energy, energy efficiency, and climate adaptation strategies by engaging students, faculty, staff, and community members in a sustainable learning community. Faculty, staff, and students at UNH serve on the Energy Task Force (ETF) – created in 2005 to help guide reductions in energy use, energy costs, and greenhouse gas emissions on campus.
We're proud of UNH's track record on energy consumption and low-carbon energy. Learn more about UNH's sustainable energy efforts below and visit UNH's Energy Office for more details.
In 2018 UNH commissioned the design and construction of its Northwest Heat Plan (NWHP), a new biomass-fired, district heat plant. The plant utilizes semi-dry woodchips, which are a new and innovative biomass fuel that is widely used in Europe but just beginning to gain adoption in the United States.
UNH is the first higher education institution to use semi-dry chips in the United States. This emerging biomass fuel type has benefits when compared to more traditional wet woodchips and wood pellets. This state-of-the-art facility provides heating hot water to five buildings totaling over 100,000 net square feet of academic and research space.

STARS EVALUATION
ENERGY (6.91/10)
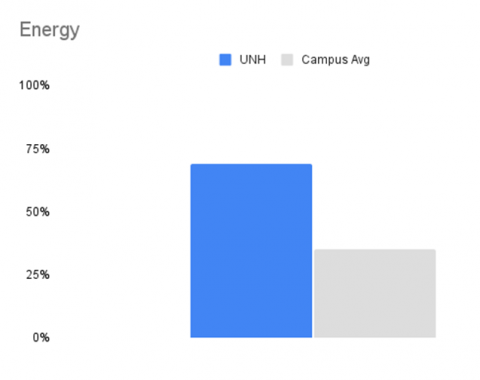
UNH earned 69.1% of total points available (6.91/10) compared to an AASHE member average of 35.34%.
STARS “seeks to recognize institutions that are reducing their energy consumption through conservation and efficiency, and [are] switching to cleaner and renewable sources of energy such as solar, wind, geothermal, and low-impact hydropower.”
Energy Initiatives
UNH's combined heat and power facility, or cogeneration (cogen), power plant is the primary source of heat and electricity for the six-million-plus square foot Durham campus. The facility was originally designed to produce only power, but UNH invested in making it a cogen facility more than a decade ago, to increase energy efficiency, cut costs and improve environmental performance. Cogen is much more efficient because it retains waste heat normally lost during the production of electricity, and instead uses this energy to heat buildings, in turn reducing harmful air pollution.
- Cost savings: UNH's cogen, including a chilled water plant, cost an estimated $28 million - all self-financed - with an anticipated payback within 20 years. These savings incorporate the avoided costs of investing in the existing plant for needed renovations.
- Emissions savings: the installation of the cogen plant resulted in an estimated reduction in greenhouse gas emissions of 21% in Academic Year (AY) 2006 compared to AY 2005.
Landfill Gas
In 2009, UNH invested in a partnership to allow it to use processed landfill gas as the primary fuel for the cogen plant. This involved partnering with Waste Management of New Hampshire, Inc. to build a pipeline, called ECOLine, of enriched and purified gas from Waste Management’s landfill in Rochester to the Durham campus. Coming from Waste Management’s Turnkey Recycling and Environmental Enterprise (TREE) facility in Rochester, NH; the landfill gas replaces commercial natural gas as the primary fuel in UNH’s cogeneration plant – and helps prevent emissions of methane from the landfill. Construction began in 2007 on the landfill gas processing plant in Rochester that purifies the gas and on the 12.7-mile underground pipeline that transports the gas from the plant to the UNH Durham campus.
UNH is the first university in the country to use landfill gas as its primary fuel source. When fully operational, ECOLine provides up to 85% of the campus's energy.
- Cost savings: ECOLine costs an estimated $49 million - all internally funded - with an anticipated payback within 10 years of the project. Both the cogen plant and the landfill gas projects were financed by the campus through borrowing.
- Renewable energy credits: In 2009, UNH began to sell the renewable energy certificates (REC's) associated with ECOLine's electricity generation to help finance the capital costs of the project and to invest in additional energy efficiency projects on campus. By selling RECs, UNH demonstrates fiscal as well as environmental responsibility.
- Emissions savings: When combined with the cogen plant, ECOLine stabilizes energy costs, provides energy security, and demonstrates environmental responsibility. ECOLine and selling RECs are part of UNH’s aggressive climate action plan called WildCAP, which outlines how the university will lower its emissions to basically zero and secure its leadership position in climate protection as part of its broader sustainability commitment.
Renewable Energy Procurement
In 2015, UNH partnered with Community Hydro to purchase approximately 20% of the electricity that we purchase. In 2016, put arrangements in place to ensure that 80-100% of the electricity that we purchase comes from renewable sources like small NH-based hydro facilities, solar, wind, or biomass.
In addition, in 2017, UNH began investing in renewable energy in yet another form: unbundled RECs produced and sold from wind farms in Texas and the Great Plains. By purchasing these Green-E certified RECs, UNH is able to support wind power that displaces more carbon intensive power generation in other regions of the country. These REC purchases help to drive costs down for clean energy projects and allow the industries to scale.
UNH is proud to be one of 17 partners to participate in the Department of Energy's Better Buildings Smart Labs Accelerator (SLA) Program. As part of that effort, we’ve committed to reducing energy use in labs by at least 20% over the next 10 years and implementing no-or low-cost measures in the shorter term. A host of partners from across the university, including The Sustainability Institute, Energy Office, Office of Environmental Health and Safety, and University Instrumentation Center have been focused on the following objectives:
- Improving the processes for introducing energy reduction activities within laboratory buildings at UNH
- Sharing of best management practices for implementing energy reduction activities
- Developing low to no-cost energy savings projects and practices in support of laboratory personnel
- Identification of code-related barriers for energy efficiency and recommend change
- Promoting UNH’s commitment and success in energy reduction activities within laboratory buildings
- Educating campus stakeholders on the benefits of implementing energy reduction initiatives in their work areas and buildings
One important effort of the SLA initiative has been to replace UNH’s ultra-low temperature freezers—which are the most energy-intensive pieces of equipment in a scientific research laboratory—with high efficiency models. This has been a systematic and collaborative program, in which the College for Life Science and Agriculture has also a key partner, that has saved the University hundreds of thousands of kWh’s and tens of thousands of dollars. UNH created a case study of this effort which is featured in the Smart Labs Accelerator Toolkit—and in 2019 the university was recognized by the National Renewable Energy Laboratory with its Accelerating Smart Labs Award for its success.
Launched in 2009 with a $650,000 grant from the American Recovery and Reinvestment Act (ARRA), UNH’s Energy Efficiency Fund (EEF) has seen more than $1,00,000 in energy savings “returns” as well as reducing many tons of carbon emissions.
How the EEF Works
The EEF is a “revolving” fund: savings from the energy efficiency projects are estimated using a combination of sub-metering and engineering estimates that follow the International Performance Measurement and Verification Protocol. Savings are captured through a System’s Benefit Charge (SBC) included in the utility costs charged to campus units. Thus a slightly higher rate offsets lower consumption due to the energy efficiency improvements and the net impact of funding the EEF on-campus units is cost neutral. Gas and electric utility companies recover similar costs from their customers using similar system benefit rate structures. The UNH Energy Office targets an average five-year payback on projects funded. Project selections are approved by the UNH Energy Task Force, which is comprised of administrators, faculty, staff and students from across campus.
The EEF has already invested in many projects, including:
- Efficient lighting retrofits across campus.
- Digital lighting controls in the main library.
- Insulating steam distribution piping.
- Upgrading a lab ventilation system in the engineering building. The building will also see one of the next investments, a passive solar heating system.
- Updated equipment in UNH's cogeneration plant.
- A retro-commissioning program which targets 5 to 20-year-old energy-intense buildings where we believe returning HVAC systems to peak performance can result in significant efficiency improvements.
History of EEF
Through the early 2000s, steady investments in energy efficiency improvements had been made as the campus leveraged its own funds with rebate programs offered by the local utility companies. However, these programs became more restrictive concurrent with UNH investing in a combined heat and power plant to better utilize on-site energy, but which essentially eliminated any remaining eligibility for rebate programs. While renovation and new construction projects continued to require high-efficiency lighting, motors, and HVAC systems, investment in pure energy efficiency projects stopped and campus energy use intensity (total energy per GSF) started to climb; an unacceptable trend for a campus with a strong culture of being “green.”
Campus energy managers, members of the Sustainability Institute, and the campus Energy Task Force (ETF) recognized that a dedicated funding stream for energy efficiency improvements was needed if the trend was to be reversed and the concept of an Energy Efficiency Fund (EEF) was developed. The fund would invest in energy efficiency improvements and the value of the estimated annual energy savings would be returned to the fund through a surcharge on the utility rate charged to campus units (UNH utilities operate as a cost center and charge campus units for utilities consumed.) This would replenish the fund and allow further investments. However, an initial source of funds needed to be found. After several unsuccessful initiatives, in 2009, UNH was able to secure a $650,000 grant of American Recovery and Reinvestment Act (ARRA) funds, and the EEF was launched.
The university requires that the energy consumption and “life-cycle impact” of equipment be taken into account when making purchases of new fixtures and equipment, and that staff and faculty look for Energy Star, E-PEAT, or other certifications whenever possible.
Also, UNH has moved away from exterior metal halide fixtures and has identified LED replacements as the new choice for walkway, street, and building exterior fixtures (section 16510 Interior Luminaries of the UNH Planning, Design and Construction Guidelines). Choice of fixtures are made with the following considerations:
- Energy efficiency and sound rating
- Quality of lighting
- Ease of installation and installation flexibility
- Ease of maintenance
- Suitability for the specific application
- Replacement parts availability
- Consideration of potential abuse
UNH has moved away from exterior metal halide fixtures and has identified LED replacements as the new choice for walkway, street, and building exterior fixtures.
UNH uses VendingMiser® technology in vending machines. Maintenance savings is generated through reduced running time of vendor components, estimated at $40 - $80 per year, per machine. Energy consumption is reduced an average of 46% -- typically $150 per machine annually.
Finally, electric hand dryers in restrooms are our campus standard for new construction and renovation. UNH is also working to escalate retrofits from paper towels to hand dryers where feasible.
See the Buildings page and UNH's Energy Office website for information about UNH’s Building Automation Systems, which are used to regulate the heating, ventilation, air conditioning, and lighting in campus buildings, and which feeds data about real-time energy and water usage into our campus energy dashboard.